Porcelain is a type of ceramic material that has been highly priced for its beauty and utility for centuries. Porcelain is made primarily from kaolin, a type of white clay, along with other materials such as feldspar and quartz. The composition may vary depending on the desired characteristics of the final product, but porcelain is known for its high levels of translucency and strength. It is fired at very high temperatures, typically between 1,200°C and 1,400°C. This high firing temperature results in a vitreous, non-porous surface that is durable and stain resistant.
Porcelain originated in China during the Eastern Han dynasty (AD 25–220). Initially, it was known as “ci,” meaning ceramics made of kaolin clay. It was later termed “porcelain” by Marco Polo during his travels in the 13th century, derived from the Italian word “porcella,” meaning cowrie shell, due to its resemblance to the smooth, white surface of these shells. Chinese porcelain, particularly from the Ming (1368–1644) and Qing (1644–1912) dynasties, is renowned for its quality and craftsmanship. It was highly priced both domestically and internationally, with significant trade routes established to export porcelain to various parts of the world.
The term “fine china” is often used interchangeably with “porcelain” to refer to high-quality tableware. In addition to the tableware, porcelain has a wide range of applications, including decorative items, tiles, electrical insulators, and even dental prosthetics. Its aesthetic appeal, durability, and ability to withstand high temperatures make it a popular choice not only in craft sector, but also in various industries.
Porcelain in Europe
The history of porcelain in Europe starts with Marco Polo. In the 14th century, the explorer brought a small jar from China back to Europe and Chinese porcelain became favored among the royalty. During the sixteenth century, the Portuguese and Dutch established commercial trade routes to China and the European market for porcelain grew fast. China kept porcelain’s ingredients and production process a closely guarded secret, inspiring scientists across Europe to experiment with materials and formulas. The first European porcelain factory was established in Saxony, Germany, in 1710 after kaolin was discovered nearby.
Porcelain: Limoges porcelain, France
In 1768, a chemist’s wife in Saint-Yrieix, a commune just outside of Limoges in southwest-central France, made a thrilling discovery: A soft white substance in the soil. At first, the story goes, the woman thought the substance could be used to wash and bleach linen, but it turned out she had stumbled upon “white gold.” The substance was kaolin, a rare and precious white clay that is a key ingredient in crafting fine porcelain. That discovery set Limoges on a path towards becoming a centre for some of the most beautiful and coveted porcelain in the world.
The first porcelain with the Limoges mark was produced in 1771. Limoges had all the essential natural ingredients needed to create world-class porcelain—kaolin, feldspar and quartz—but, just as importantly, the region had a vibrant history of craftsmanship that dated back nearly a millennium. In the 12th century, Limoges was the most famous European centre of vitreous enamel production, known as “Opus de Limogia” or “Labor Limogiae“. Limoges also produced faience earthenware or fine in-glazed pottery. The heritage of ceramics and decoration was deeply woven into the fabric of the city.
Making porcelain is a difficult, delicate, and time-intensive process that involves vitrifying the clay multiple times at extremely high temperatures. Limoges porcelain is known for its dazzling white, luminous hue and the intricacy of its hand-painted decorations. At first, its manufacture was placed under the protection of the Comte d’Artois, Louis XVI’s brother, and then purchased by the King himself. It became the Manufacture Royale de Limoges, with the exclusive right to produce Limoges porcelain for the Kingdom of France. In Louis XVI’s time, the manufacturer primarily produced trinket boxes of varying shapes and sizes depending on what they were meant to hold, from embroidery scissors to snuff powder to poems. Popular design styles included Rococo-style figures; exotic birds, flowers, and marine subjects on bright colour backgrounds; minute patterns embellished in gold; and narrative scenes from classical mythology and pastoral life.
After the French Revolution, the restrictions on porcelain production were lifted and commercial trade flourished. In 1819, the region had four porcelain factories; by 1900, there were 35 factories and 120 kilns employing up to 8,000 workers. Limoges became the undisputed French capital of porcelain production, as well as a major exporter of porcelain to the U.S.
Centuries later, Limoges porcelain continues to signal luxury and refinement. Limoges objects and dinnerware collections are commissioned by presidents and royalty and passed down through generations in families, but the industry continues to push creative boundaries that maintain porcelain’s relevance.
Limoges porcelain has always married the beautiful with the functional. Some applications of porcelain draw on the material’s unique properties of strength, durability, and imperviousness to create products that enhance everyday life. Thanks to its unique geologic and design history, Limoges is a global centre that showcases all the possibilities of what porcelain can be.
Safeguarding history
Musée national Adrien Dubouché in Limoges stands as the guardian of history, safeguarding the legacy of Limoges porcelain. With the most extensive public collection of Limoges porcelain worldwide, it preserves the artistry of centuries past while illuminating the evolution of ceramics from Antiquity to the contemporary era. Housing a remarkable ensemble of 18,000 works, 5,000 of which are presently showcased, the museum orchestrates a journey through time.
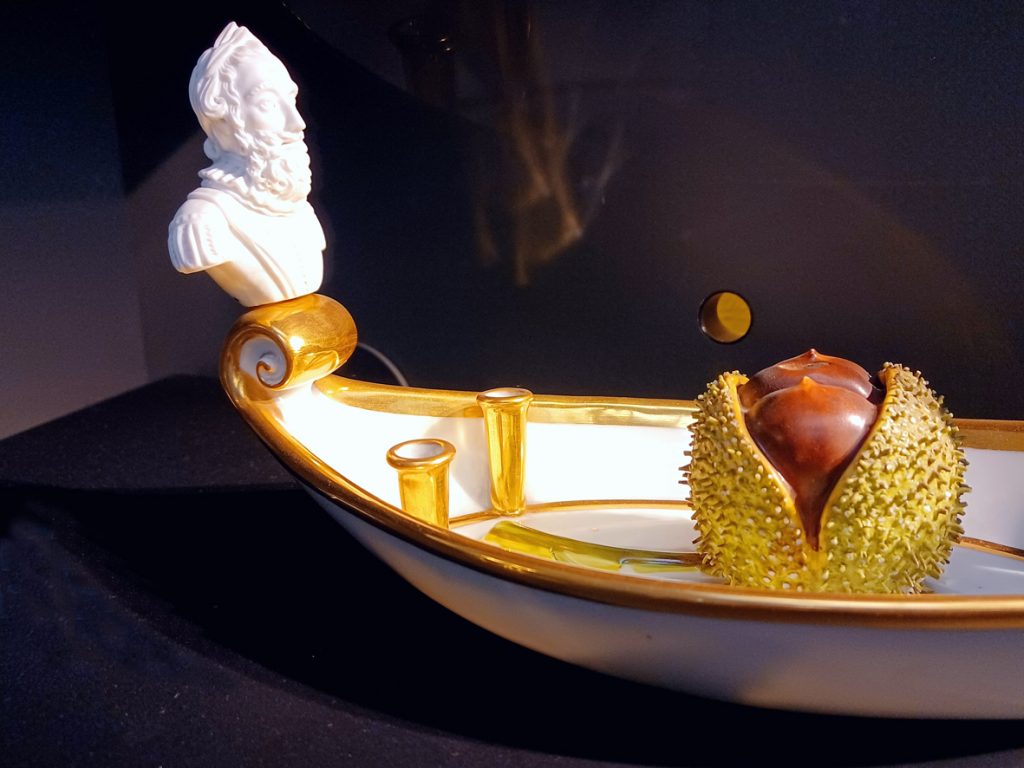
Credit: Madina Benvenuti, MDE (2024). Encrier en forme de chataigne offert a la duchesse de Berry Manufacture Pierre Tharaud Limoges 1828 red in Musée national Adrien Dubouché.
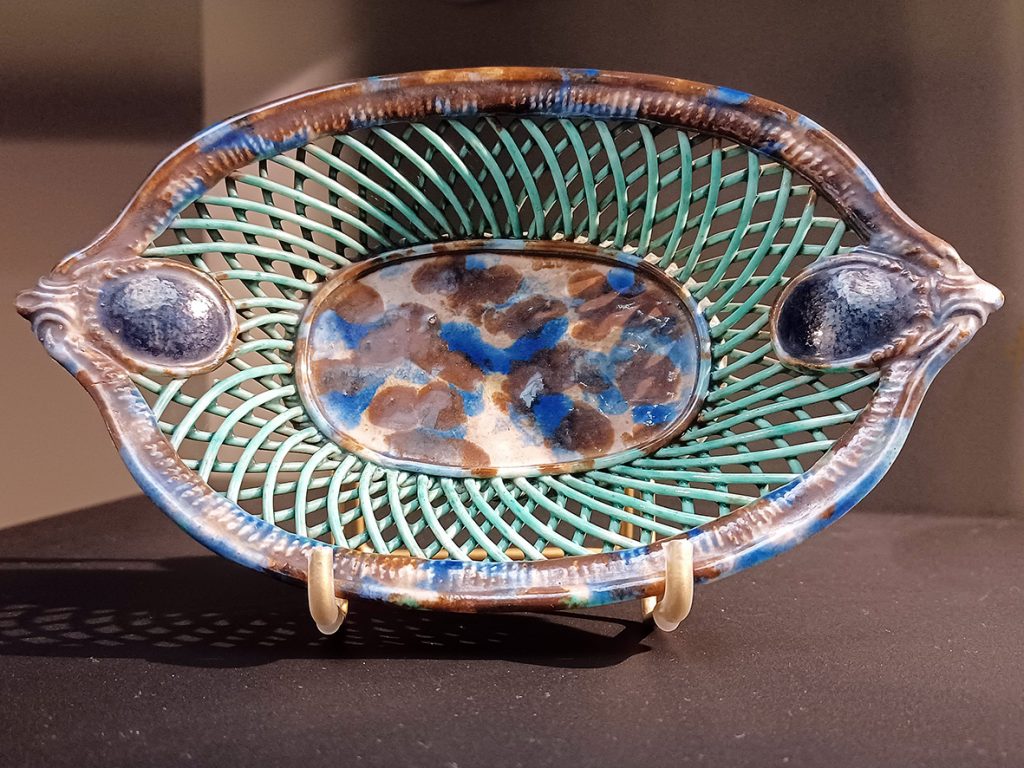
Credit: Madina Benvenuti, MDE (2024). Corbeille ajourée Manufacture_Lesme Limoges vers 1850 in Musée national Adrien Dubouché.
Transmitting tradition
Since its establishment in 1962, Ecole Nationale Supérieure d’Art et de Design (ENSAD) has been preserving and transmitting on the enduring legacy of Limoges porcelain. Not only does ENSAD uphold tradition, but it also serves as a hub for innovation and creativity, guiding Limoges porcelain into the future. Through research and experimentation, ENSAD fosters new ideas and techniques, expanding the possibilities of this esteemed material. Recognizing Limoges porcelain as a cultural symbol, deeply rooted in the region’s identity, ENSAD celebrates its significance, instilling pride and appreciation in the local community. By training skilled artisans and designers, ENSAD contributes to the local economy, ensuring the ongoing prosperity of the porcelain production.
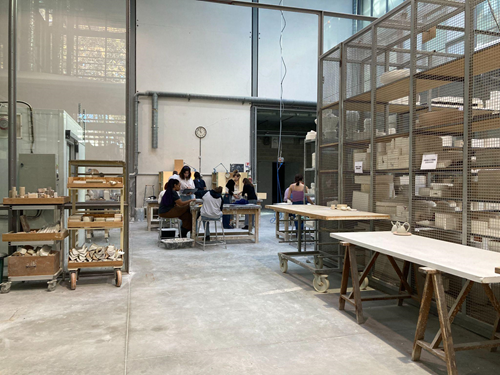
Credit: Arnaud Dubois, CNAM (2023). Atmosphere at – Ecole Nationale Supérieure d’Art et de Design of Limoges.
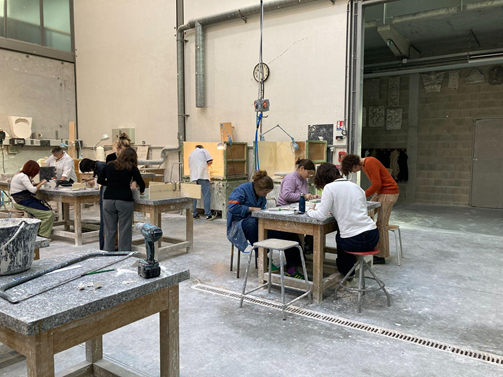
Credit: Arnaud Dubois, CNAM (2023). Atmosphere at – Ecole Nationale Supérieure d’Art et de Design of Limoges.
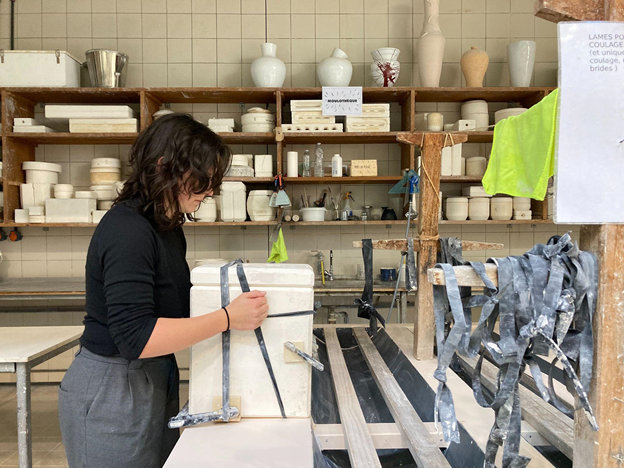
Credit: Arnaud Dubois, CNAM (2023). Making process in Ecole Nationale Supérieure d’Art et de Design of Limoges.
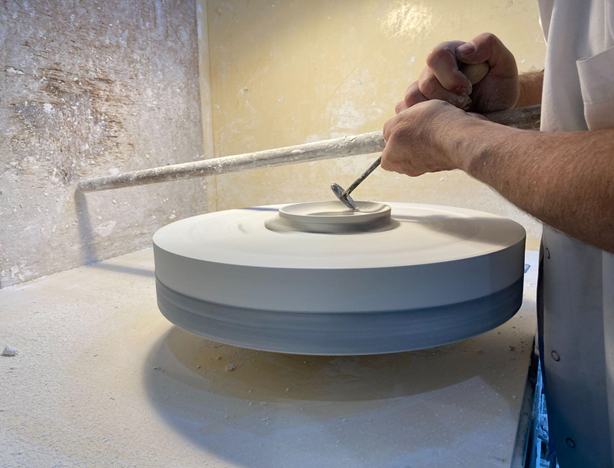
Credit: Arnaud Dubois, CNAM (2023). Detail of the making process in Ecole Nationale Supérieure d’Art et de Design of Limoges.