The CRAEFT team, made of Arnaud Dubois, anthropologist from CNAM, Sotiris Manitsaris and Gavriela Senteri from ARMINES and Madina Benvenuti form Mad’in Europe, spent 2 days at the École Nationale Supérieure d’Art et de Design de Limoges (ENSAD) school to record gestures and understand how fire transforms a liquid mixture made of water, kaolin, feldspar and quartz into porcelain.
Marie Laure Trochon and Gilles Bonettat guided us, from the sketch to the model making, up to the final product, step by step, letting us observe the negotiation between makers and raw material. They kindly accepted to let our team record their hands at work with an egocentric camera and participated in the video elicitation with our team, explaining in detail each of their gestures. They also introduced us to the secrets of porcelain making from the model to the firing.
Credit: Madina Benvenuti, Mad’in Europe (2024). Video introduction – Marie Laure Trochon.
Marie Laure Trochon is a ceramic modeller, her work consists of making models from technical drawings produced by designers. After making the plaster model, she casts a test piece which is then glazed and fired. If the piece is approved, she can move on to making the final matrix, the “mould of the mould” that enables mass production.
Credit: Madina Benvenuti, Mad’in Europe (2024). Video introduction – Gilles Bonettat.
Gilles Bonettat technician in the pedagogical team of ENSAD, in charge of the porcelain workshop and specialist of the “blanc de blanc” production, a porcelain fired at 1380 Celsius degrees, a process which produces the transparency and bluish hue for which Limoges porcelain is renowned.
Recordings of the making processes
During the visit to ESNAD the following processes of porcelain making were documented:
FETTLING or REMOVAL of SEAM LINES: Fettling involves removing excess clay and smoothing out seams or imperfections that occur during the moulding process. It ensures the piece has a clean and finished appearance.
Credit: Gavriela Senteri, ARMINES (2024). First-person view of Marie Laure Trochon fettling.
SLIP CASTING: Slip casting is a technique where liquid clay (slip) is poured into a plaster mould. As the mould absorbs water from the slip, a layer of solid clay forms against the mould’s surface, creating the shape of the ceramic piece. Once set, the mould is removed, and the piece undergoes further drying and finishing processes.
Credit: Gavriela Senteri, ARMINES (2024). First-person view of Gilles Bonettat slip casting.
JOINING the HANDLES: This refers to the process of attaching handles to ceramic pieces, such as cups or pots. Handles are usually moulded separately and then joined to the main body of the piece using slip (liquid clay) as an adhesive. Careful handling and shaping ensure the handle is securely attached and aesthetically integrated into the piece.
Credit: Gavriela Senteri, ARMINES (2024). First-person view of Marie Laure joining the handles.
PLASTER TURNING ON A WHEEL: This refers to the process where a ceramic piece is turned on a lathe made from plaster moulds. It is typically used to refine the shape and smooth the surface of the piece.
Setting the work position: Marie Laure secures the «pichouret» (long wooden stick) between the abdomen and the wheel base to increase stability. The body leans slightly forward, with feet apart and toes pointing outward. Marking and measuring the reference points: Holding the «pichouret» in place, she marks a circle using a pencil while slowly rotating the wheel. Ensures precision by stabilising the pencil between the thumb and forefinger. Checks the accuracy of the circle with a compass.
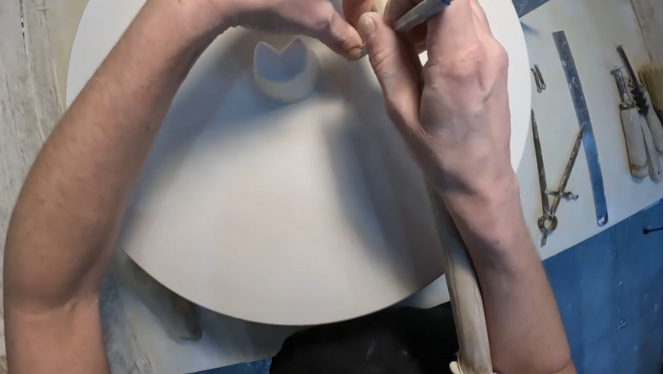
Marking a circle.
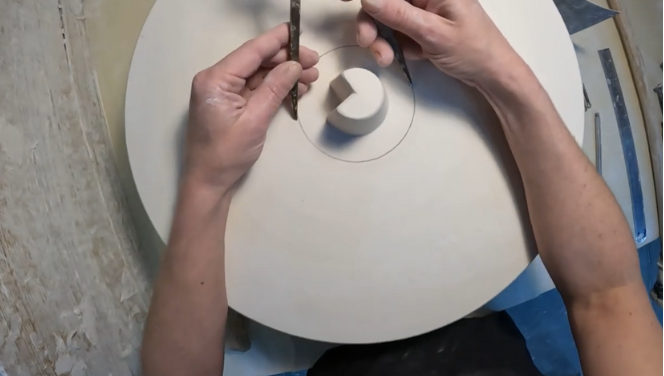
Checking the accuracy of the circle.
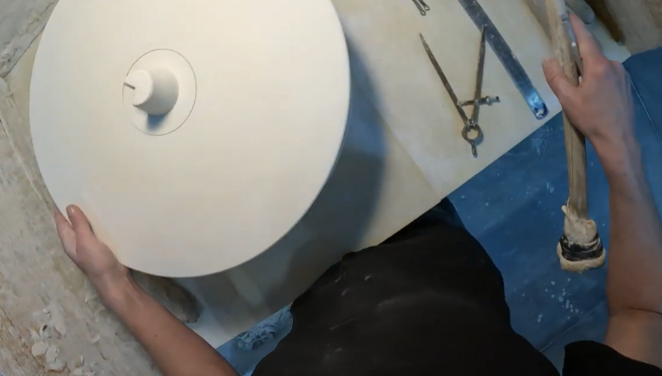
Circle is marked.
Applying soap for smooth turning: Marie Laure uses a large brush to apply soap solution to the turning plate in circular motions. Excess soap is removed by twisting the brush bristles between her hands. Minute in the video: 0’50” – 1’27” Fixing the formwork to the plate: The formwork is carefully positioned around the reference circle and clipped into place. A moist clay coil is shaped, flattened, and pressed against the base of the formwork while rotating the plate with one hand for even distribution. Minute in the video: 2’08” – 3’50”
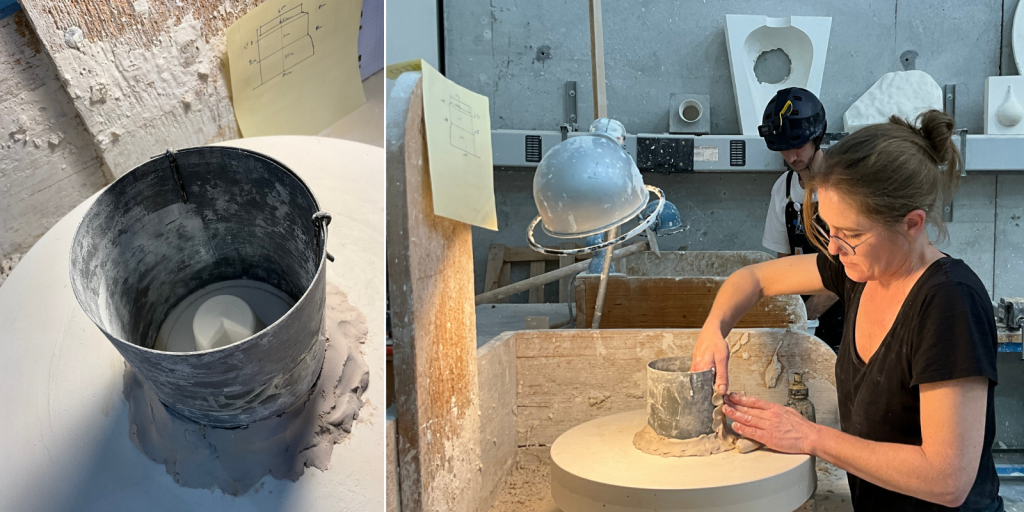
Credit: Madina Benvenuti, Mad’in Europe (2024). Marie Laure Trocho – Fixing the formwork to the plate.
Checking plaster consistency: Touches the plaster inside the formwork with her ring finger to assess if it is ready for shaping. Minute in the video: 4’15” – 13’20” Pours in the plaster At 13’31” Removing the formwork: While turning the wheel with her left hand, she carefully removes the clay securing the formwork. Cleans any excess plaster with a scraper, ensuring a smooth surface for shaping. Minute in the video: 16’20” – 17’00” Plaster carving Starts at 17’00”
Credit: Gavriela Senteri, ARMINES (2024). First-person view of Marie Laure Trochon plaster turning on a wheel.
Credit: Gavriela Senteri, ARMINES (2024). Third-person view of Marie Laure Trochon plaster turning on a wheel.
This sequence highlights the delicate balance of hand coordination, tool precision, and controlled wheel movement, essential for shaping plaster on a turning wheel. It is a simplified yet still highly effective demonstration of the craftsmanship required in this process.
Watch the video to see how we spent the day in ENSAD
Credit: Mad’in Europe (2024). Video – A Day in the Life of ENSAD.